Made in Tartaruga
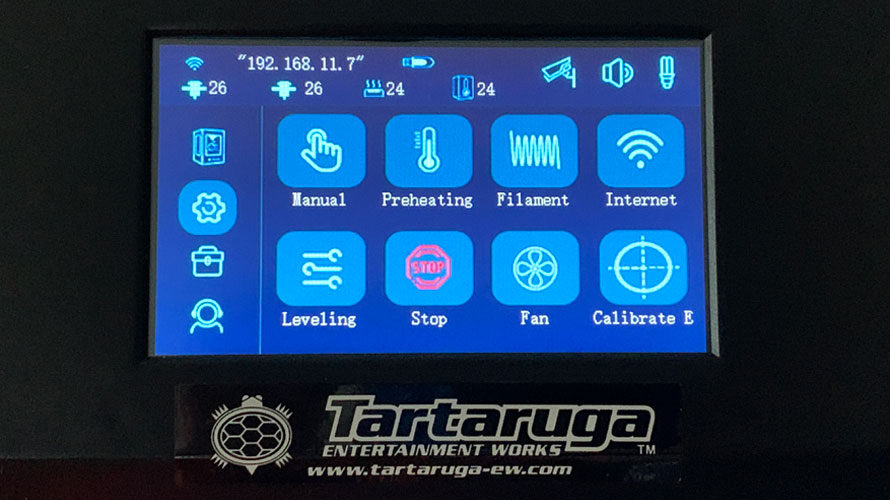
世界的な、自転車需要の急拡大と、パンデミック等
様々な影響から、素材やパーツの入手困難が続いています。
また、弊社が生産を委託している台湾のPacific 社をはじめ、世界中の自転車生産工場も、大量受注により生産ラインに空きが無く、現在、弊社製品の次回生産は、2023年の秋以降との予定となっています。
これは、自転車業界に限った話ではなく、様々な業界で、工業製品の生産がままならない状況が、しばらく続きそうな雰囲気が、世界中で広がっています。
ならどうする?
「自社工場を建てよう!」
と、いう訳には、なかなか現実的に行きません。
思案した結果、「マイクロ自社工場」として、「ちょっとイイ3Dプリンター」を社内に導入して、製品自体を社内で「3Dプリント」してしまおうという結論にいたりました。
現在、弊社でのデザイン作業は、最終的に殆ど3D CADでのデータ制作まで行っています。
3D データを作るわけなので、「そのデータをプリントすればいいだけだ!」と考えたのですが、実際に導入してみると、それほど「簡単」なものではありませんでした。
プリンターの選定
3Dプリンターは、ここ数年で、飛躍的な進化と、ローコスト化が進み、とても身近な存在となってきました。
実は、数年前にも一度、弊社への導入を検討した時期がありましたが、当時はまだまだ高価で、高価な割には印刷物のクオリティーは、まだまだ私の要求を満たすものではなく、その時は導入を見送りました。
改めて現在の3Dプリンター市場を調べてみると、数万円クラスから小型の試作品レベルの実用に、耐えられそうな物がある事に驚きはしましたが、「マイクロ自社工場」を目指す観点から、ネット上の情報等を物色しまくった結果、「インダストリアルグレード」と呼ばれる商品群の中では、比較的安価で、「サポートが、とてもしっかりしている。」と評判の「QIDI TECH 社」製の「i-fast」という機種を導入することにしました。
QIDI TECH i-fast
2022年1月に、この時点での最新バージョンの「i-fast」が届き、使用を開始しました。
最大330㎜×320㎜×250㎜のサイズまでプリント可能なこの機種は、プリンター自体かなり巨大で、重量も33キロ以上とヘビー級です。
なにより、3Dプリンター自体を触るのが初めてで、何の予備知識も持ち合わせていなかったため、「スライサー」と呼ばれる、製品付属のソフト「QIDI Print」の扱い方を、一から学ぶ必要に迫られました。
このソフトは、「Cura」という現在最も広く使用されているスライサーソフトを、QIDI TECH 社が自社製品用にカスタマイズしたもので、幸い「Cura」に関する情報(殆ど英語なのですが・・・)がネット上にたくさんあり、わからない事は、都度検索したり、サポートに問い合わせたりしながら、学びました。
弊社のクライアント向けデザイン作業で、例えば「握り心地」の検討などには、CAD上の3Dデータだけでは、全く検証のしようがありませんでしたが、試作品をサクッとプリントしてしまえば、簡単にリアルな検証が行え、そのアドバンテージを直ぐに教授することになりました。
フィラメント(素材)
弊社の導入した3Dプリンターは、現在最も一般的なFDM方式(熱溶解方式)というタイプで、「フィラメント」と呼ばれる、ロールに巻かれたヒモ状の樹脂を、熱で溶かしながら積層していくタイプです。
最も3Dプリンターに向いていると言われている「PLA」という素材でプリントする分には、「QIDI Print」のデフォルト設定で、結構簡単に、とても優れたプリント結果を得ることができました。
「PLA」は、形状確認や、試作レベルのプリントであれば、とても優れた素材なのですが、熱変形温度が低いため熱に弱く、また、強度等の機械特性もあまり高くない為、製品に使用することは、あまり現実的ではありません。
今回のメインの目的は、あくまでも弊社 Tartaruga シリーズのオプションパーツとして、実用に足りるオリジナル製品を製作する事にありました。
野外での使用が前提となるため、耐紫外線性能などの、耐候性も求められます。
3Dプリンター用のフィラメント素材で、この要求を満たせるのは「ASA」という、「ABS」の一部配合を変えた特殊素材が、一番向いているといるとの結論に至ったのですが、比較的新しい素材なため、日本国内には情報を含め、あまり出回っておらず、値段も高価です。
スライサーソフトに、「ASA」のデフォルト設定自体もありません。
また、物性的に大変センシティブな素材のため、フィラメントのブランドごとにプリント設定が大きく異なるなど、とても扱いが難しい素材でした。
「QIDI Print」の「ABS」の設定をベースに、各種パラメーターを調整することになるのですが、とんでもなく多くのパラメーターを調整できるため、途方に暮れる日々がしばらく続き、何をどう変更すると、プリント結果としてどう変わるのかを、「ある程度」把握するのに、2カ月近く掛かってしまいました。
フィラメントの乾燥
フィラメントの取扱い上の注意点、もう1点とても大事なことが、乾燥でした。
プリントが容易と言われる、「PLA」を使ったプリントでも、急に外観に「糸引き」の様な現象が発生し、その原因を調べたところ、素材の「吸湿」が原因でした。
一度「吸湿」したフィラメントは、乾燥機で乾燥する必要があり、この乾燥の温度や時間も素材ごとに異なります。
結局最初に購入した、フィラメントドライヤー(専用の乾燥機)では、ASA の乾燥までの性能が無く、もうワンランク上のドライヤーを追加購入しました。
また、使用したフィラメントの保管も、真空にできるバッグを購入して、使い終わったら都度、乾燥材と一緒に真空パックにして保管しておかないと、空気中の湿気をあっという間に吸湿して、劣化してしまいます。
あれやこれやと、関連する機材や道具が、必要に迫られどんどんと増えていきましたが、ようやく満足のいくプリント結果が得られるレベルに使いこなせるようになりました。
Tartaruga In-house production series
といった経緯をたどり、Made in Tartaruga と言える、「Tartaruga In-house production series」の発売を、近々開始いたします。
これまで型代負担の制約や、ミニマムロット(最低生産数量)等の問題から、なかなか実現できなかった「本当に細かな商品」が中心です。
また、綺麗なプリント結果を得るには、時間を掛けてプリントする必要があり、結果的に多少お値段が高めの設定となってはしまいますが、「より良い製品」を優先して皆さんに提供できるようにしたいと考えています。
準備が整いましたら、改めてお知らせいたしますので、今しばらくお待ちください。
-
前の記事
キャンプツーリング in 奥多摩 2022春(後編) 2022.04.19
-
次の記事
Tartaruga In-house production series 第一弾 2022.06.24